Section 1.10 - Pressure Control
(Pressure limiting device-relief valves)

Function
To limit the pressure of some section of the hydraulic system when the pressure has
reached a predetermined level. That pressure level may be considered dangerous and,
therefore, must be limited.
Principle of Operation
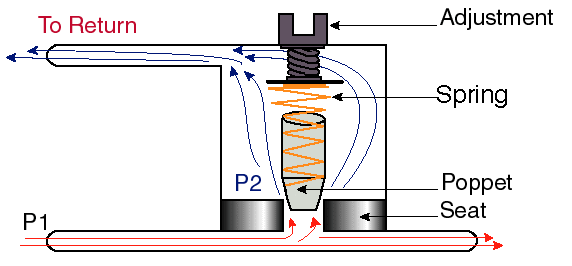
The adjustment screw at the top of the pressure relief valve is set for a certain
pressure value, let us call it P2. In general, even with a pressure of P1,
the poppet would lift up, except that the spring is strong and has downward force forcing
the poppet closed. Poppet will not move until a pressure greater than that required is
felt by the system (i.e., P1>P2). When the pressure increases,
the poppet will move up, forcing the excess liquid to move through opening at high
velocity. On other side of seat, pressure is zero because the back side of the relief
valve is connected to the return line. When the pressure in the system decreases below
maximum, poppet will return to its seated position, sealing the orifice and allowing the
fluid to follow its normal path. These type of pressure relief valves are only made to be
used intermittently.
Design Example
An example of designing the spring required for a poppet valve--
If the frontal area of the poppet is 1/3 square inches and the liquid pressure is at
6000 psi, find the spring force required to keep the poppet shut.
The frontal area is the effective area on which the fluid pressure acts. Even if the
poppet sides are slanted, the pressure acts normal to that surface area, producing forces
normal to that surface area. These forces can be resolved into force components
perpendicular to the flow direction and force components parallel to the flow direction.
The force components that are perpendicular to the flow direction for both the top slant
face and bottom slant face cancel. The force components that are parallel to the flow
direction for the top slant face and bottom slant face add.
This is equivalent to finding the area that the poppet seats and multiplying it by the
pressure of the fluid, namely, 
Circuits Using Pressuring Limiting Devices (PLDs)
- The power system where the system relief valve is used to back up the regulator
is an example of a use of the PLD. In such a system, the pressure setting, P2,
is set 125% above the system pressure. Rate of flow is dependent upon engine speed.
- Thermal relief valves are set at 150% of system pressure. When the temperature
(T) changes, the liquid expands more than the expansion of the hydraulic tubing. Since T
increases, the pressure (P) increases. Thus, the tubing will burst unless there are
thermal relief valves in the system. Set at one pressure, the thermal relief valves are
connected to the return lines because the pressure there is close to nil. This only works
when the selector valve is set in the neutral position.
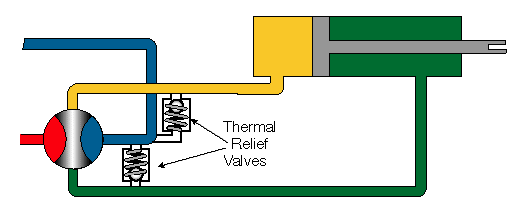
- Force Limiting Device (FLD). Suppose that we want 1000 pounds of force to move a
certain control surface. But our system can deliver 3000 pounds per square inch. If that
pressure can be delivered on a 2 square inch piston head that moves the control surface,
we would be= 6000 lb, a much higher force than is needed. We can put a force limiting
relief valve (FLD) which would limit the force to 1000 lb by adjusting the FLD to act when
the pressure reaches 500 psi (1000 lb/ 2 square inches). After the FLD is used, you need
to put the selector valve at neutral so that no system pressure will be lost.
- Force limiting circuits for gun chargers. When a gun is fired and a bad shell is
put into the gun, the gun will stop working. Gun chargers do the work of removing the bad
shell and then replacing it with a new shell, pulling the charging handle back, and the
gun will be ready to fire again. The gun charger FLD is set so that a minimum force is
used to pull the charging handle back.
- Blow up devices. When a plane is coming in for landing on a carrier deck, the
brakes are set and the selector valve is put at neutral. If the plane is waved off on its
landing attempt, the brakes must retract quickly so that the plane does not stall.
Therefore, when the pilot is waved off, he will push the throttle to get more speed to get
away from carrier. In doing so, the air pressure force acting on the brakes, F, is so
great that it moves the brake. In doing so, the piston moves to right, causing fluid to
flow (in the red line) and to push on the relief valve. This action allows more oil into
the other line (the white line) which in turn pushes on the piston and repeats the
process. After the pilot reacts to this situation, he will change the selector valve
position (if he has to change it), to move the brake back into its non-deployed position.
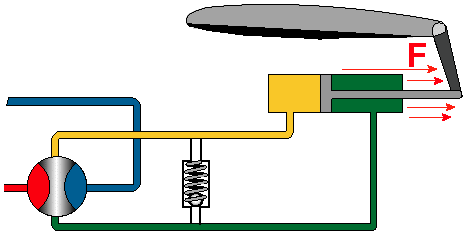
Send all comments to
aeromaster@eng.fiu.edu
© 1995-98 ALLSTAR Network. All rights reserved worldwide.
Funded in part by |
 |
Updated: February 23, 1999